国内大手製造業A社は、産業機械向け部品を2カ所の工場で製造していましたが、増産を目指して製造力を強化するプロジェクトを計画。製造拠点を1カ所に集約し、製造ラインの移設や新設、システムの構成やレイアウトの見直しをはかることにしました。
増産に向けた効率化・環境改善お客様の増産プロジェクトで、現場の効率化・環境改善を実現
プロジェクト概要
部品の増産に向けて製造拠点を1つに集約するお客様の計画に沿うように、製造ラインの移設・新設・レイアウト変更を実施。併せて設備環境の改善を実現し、お客様の目標達成に貢献しました。
プロジェクト連携部門
プロジェクト内容
増産に向けて、製造ラインの移設・新設、レイアウトの見直しを実施したい
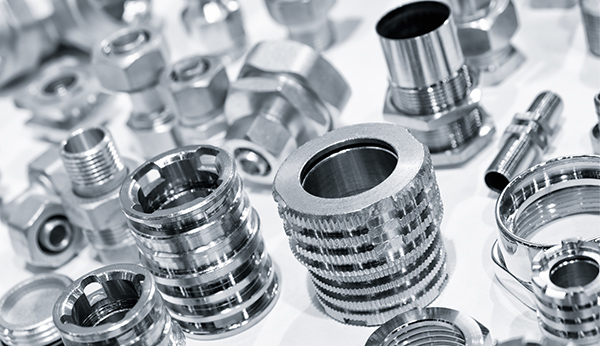
また、A社では同部品の製造ラインでエアー搬送設備を取り入れていましたが、以下のような問題を抱えていました。
- 搬送設備間で部品が引っかかり、思うように搬送できず時間がかかっていた
- エアーによる油はねが多く、設備が汚れやすくなっていた
- オイルミストが飛散し、床が滑りやすくなり転倒する恐れがあった
A社としては、まず製造ラインの移設や新設を優先して実施し、部品の製造を再開させた後で、徐々にこうした問題の解決もはかっていきたいと考えていました。
このプロジェクトの実施に際して、A社は長年にわたる付き合いにより、自社の業務に豊富な知見やノウハウを持つ岡本工業に依頼。今回は、製造ラインの設備検討・設計・製作・据え付けまでを担うFA事業部に、相談を持ちかけました。
綿密な情報連携で、お客様のご要望に合わせた、より良い製造環境を実現
構想から施工までを約半年という短期間での納品をA社が希望していたことから、FA事業部は、図面作成・材料発注・下請業者への部品製作依頼などの準備を迅速に進めました。また、エアー搬送設備の代わりに導入するコンベア搬送設備の製作では、想定外のトラブルや製作上の個体差により発生する修正や調整を、できるだけ事前に実施しておくため何度も試運転立ち会いを実施しました。
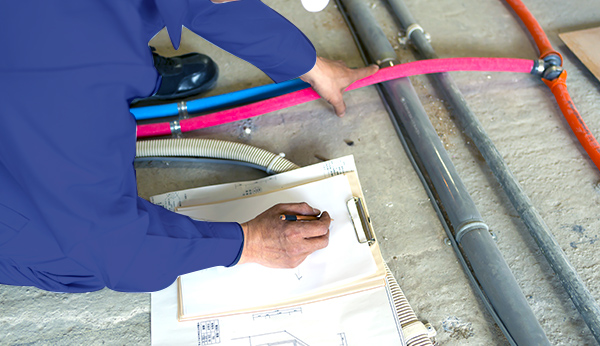
そして、今回製造した設備の据え付けは、A社工場に常駐している生産支援事業部が担当。現地の給水・給電設備の確保から施工後のフォローまで、現場施工に関することは全て同部が実施しました。
FA事業部から生産支援事業部への引き継ぎは、岡本工業内でもスタンダードなケースで、これまでに何度も行われてきました。しかし、今回担当した製造ラインの設備は、わずかなミスがラインの停止、ひいてはA社の大損害にもつながりかねません。そこで、通常よりも丁寧かつ綿密に情報連携を実施しました。そこには、FA事業部が持つ長年にわたるA社との付き合いから得た知見やノウハウを、今後の設備保全に活かしたいという思いも込められていました。
新たな搬送設備の導入で問題を解決、製造効率を向上しお客様の増産に貢献
既存製造ラインの移設後、コンベア搬送設備を含む2つの製造ラインを新設し試運転したところ、問題だった部品の搬送や、油はねやオイルミストによる設備の汚れや環境の悪化が解消。A社ではこの効果を高く評価し、追加で10ライン、合計12ラインの製作を岡本工業に発注しました。
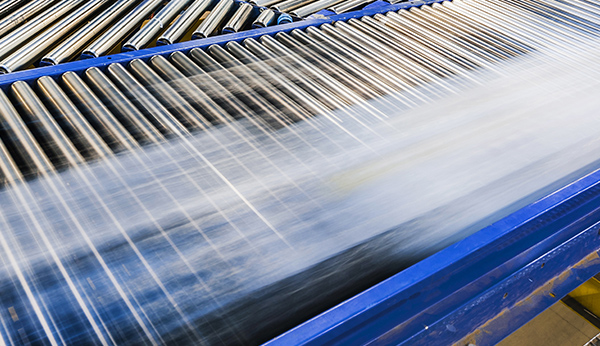
現在では、部品をスムーズに搬送できるようになったほか、ランニングコストの削減(エアー消費量削減)、生産性の向上、油はねやオイルミストが削減でき、増産という目的の達成に大きく貢献することができました。A社はこの点において、岡本工業を高く評価しています。
しかし、A社とのお付き合いは今後も継続していきます。時代の変化に伴いA社からの要望も多様化していくことでしょう。今回のプロジェクトで得た新しい知見やノウハウを活かすことで、あらゆる要望に柔軟かつ迅速に対応できるようになると、岡本工業は考えています。
また、設備のトラブルは突然発生します。これまではトラブル発生後に素早く対応することが求められましたが、今後はトラブルを予防することが求められます。突発修理を避けられるよう、予防保全計画を立案できるようA社に働きかけています。