国内大手製造業B社は、急に発生する工場設備の故障に困っていました。ひとたび故障すれば製造ラインは止まり、大きな損害が発生します。加えて、突発的な修理工事はコストが高い上、工事計画書が不十分なまま業者に修理対応を依頼することになり、安全面でのリスクも大きくなります。
IoTで設備稼働状況を「見える化」IoTを活用し、設備の稼働状況を簡潔に把握できる環境を構築
プロジェクト概要
急な設備故障を予防するため、日常的に工場内を点検して回っていたお客様。より効率的に設備の稼働状況を把握できるよう、IoTを活用した計測システム構築しました。これにより予防保全の実現にも寄与しています。
プロジェクト連携部門
プロジェクト内容
より効率的に付帯設備の状況を把握し、急な設備故障をできるだけ予防したい
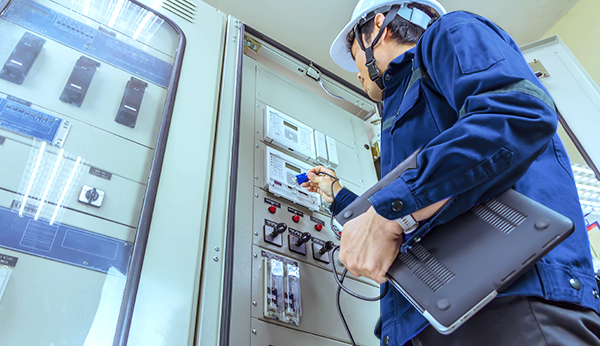
これまでB社は突発的な故障を避けるため、タンクやポンプ、コンプレッサーなど、工場内に点在する付帯設備を日常的に点検し、それぞれの温度計や圧力計の数値を目視したり、動作音や振動音などを聞いたりして、異常がないかをチェックしていました。ただ、広い工場内をそれぞれの場所に出向いて1つずつ点検して回るのに、かなりの労力がかかっていたのです。
そこで、こうした付帯設備の状況を数値として見える化し、それを1カ所でまとめて確認できないか、と考えていました。
この計画の実施に際してB社は、自社の工場に常駐し工場設備に関するあらゆる業務をサポートしている岡本工業の生産支援事業部に相談。B社の事業継続や安全に対する意識を、広く世間にアピールできるような、画期的な施策の提案を依頼しました。
IoTを活用した計測システム構築で、設備の状況を簡潔に見える化
B社は、はじめに数カ所の設備を見える化の対象とし、段階的に対象設備を増やし、最終的に工場内の全付帯設備を網羅することを計画。岡本工業は、この依頼に対して生産支援事業部・技術本部・情報システムが連携し、IoTを利用した計測システムを提案しました。まずは技術本部が中心となり、要望に合わせて検討書や図面を作成。コストや性能を踏まえた機器選定ののち、センサーを扱う協力会社2社と現場での試作を実施しました。
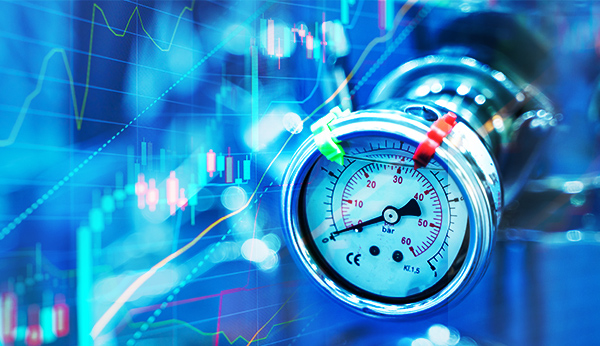
情報システムは、センサーから得たデータを管理するシステムの導入、そのシステムに必要なインフラ基盤の調達やテストなどを担当。生産支援事業部は、送信機や受信機、振動計器や熱電対、圧力計器など、設備ごとに一品一様な機器の取り付けを行いました。
計測データは無線で送受信するのですが、地下ピットにある付帯設備とうまくやり取りできないことがあり、機器の見直しのほか取り付け位置や角度を調整しました。また、グラフィック活用や2画面表示など、データの表示方法について急な仕様変更が発生し、急いで再調達や画面調整を行いました。
このように想定外の問題にも直面した本プロジェクトでしたが、3部門が一体となって細かなところまで気を配り合ったおかげで、期日通りの納品が実現できました。
設備の稼働状況を分かりやすく表示可能になり、故障の予防にも寄与
B社では、これまで人の手で計測・記録していた付帯設備の状況を、数値化した上で自動的に収集できるようになりました。特に、一部の設備では従来測定していなかった振動に関するデータも記録できています。収集したデータは分かりやすくグラフ化してから表示。誰もが日ごとの稼働状況を把握できるようになりました。
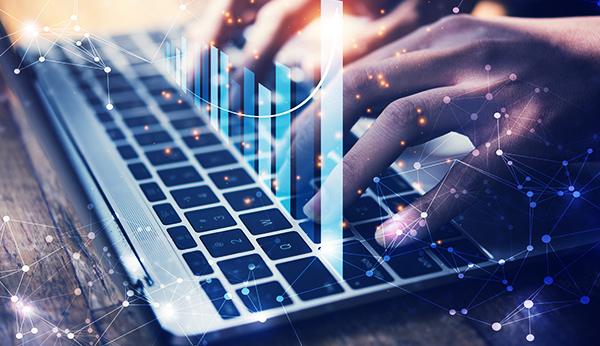
このデータを引き続き収集・解析していくことで、設備の故障につながるデータ傾向が見えてくるかもしれません。そうすれば、従来のような一定期間の経過や属人的な判断を契機としたメンテナンスではなく、データ傾向に基づいて故障前にメンテナンスを実施できるようになります。B社が目指す、設備故障を予防する「攻めの保全」の実現に近づけることでしょう。
本プロジェクトは現在、1回目の工事が完了して、2回目の工事が継続中です。3回目の工事もB社から依頼がありました。岡本工業は、これまでの工事で得た知見を今後の工事に活かしつつ、引き続き突然の設備故障を極力避けられるよう、支援を続けていきます。